Catalysis for the Circular Economy and Sustainable Manufacturing
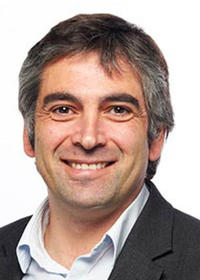
Led by Professor Matthew Davidson
The program focussed on the following areas:
-
New cooperative catalysts for C-C bond forming reactions from CO2;
-
Activation of C-O bonds for valorisation of bio-derived feedstocks;
-
Using and understanding sustainable catalytic oxidation processes in flow;
-
Earth-abundant metals in resource efficient catalysis; Keeping platform molecules in play: catalytic chemical recycling of polymers; New sustainable polymer architectures for high performance plastics;
-
Optimising bio-based platform molecules: establishing diformyl furan as a bio-based platform for polymers
A traditional linear approach to production and consumption (take, make, dispose) is unsustainable. New circular approaches (make, use, return) are growing in influence and importance with global economic growth and urbanisation. Advances in catalysis central to the circular concept of “keeping the molecules in play”. Using waste CO2, plastics recycle/reuse, bio-based resources, non toxic and abundant additives, and elimination of waste from processes all rely on new catalytic science.
Within industry, closed-loop, circular value chains and sustainable manufacturing are increasingly recognised as vital to future innovation and growth. So far, technical aspects of the Circular Economy have lagged behind the political capital. This project put UK catalytic science and engineering at the centre of the transition to a Circular Economy. It used the application of catalysis to develop circular and sustainable molecules, materials and processes across the chemicals and chemistry-using industries. In particular, the seven work packages outlined below provided catalytic solutions that will (in the words of Dow Chemical’s Chief Sustainability Officer) “keep the molecules in play”. In order to realise the circular economy, more sustainable manufacturing processes are required and there is an imperative need to develop new catalysts and catalytic processes across a diverse range of the chemicals, materials and pharmaceuticals supply chains.
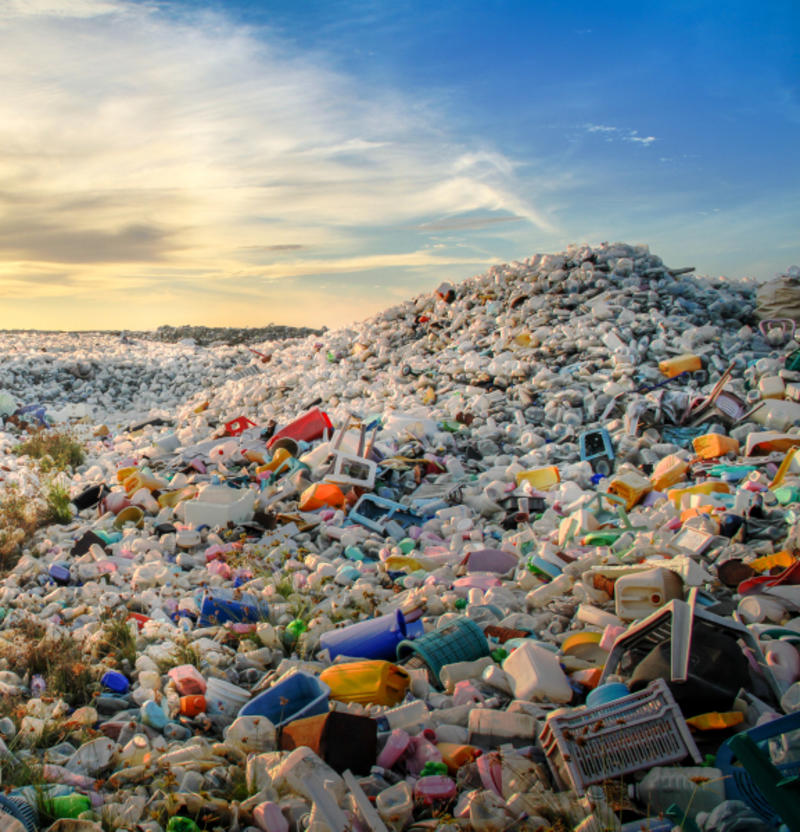
image credit: aryfahmed – stock.adobe.com
WP1: New cooperative catalysts for C-C bond forming reactions from CO2 (Leads: Aldridge (Oxford), Wass, (Cardiff))
The use of carbon dioxide as a chemical feedstock represents a highly attractive component of strategies aimed at the development of a circular economy. This molecule is almost invariably the thermodynamic end-point of any carbon-containing product, whether that is combustion as a fuel or incineration of waste, and methodologies to convert that carbon dioxide back into useful materials or precursors therefore close the largest loop of a circular economy. The conversion of carbon dioxide also represents one of the foremost fundamental technical and academic challenges of modern catalysis, with new approaches needed to unlock the potential of this area.
WP2: Activation of C-O bonds for utilization of bio-derived feedstocks (Leads: Blacker (Leeds), Hii (Imperial College))
Using renewable feedstocks is key to promoting a circular economy. While petrochemicals contain mainly C-H and C-C bonds, biomass contains C-O bonds that need to be selectively manipulated to produce useful materials. While conversions of biomass into syn gas and platform/commodity chemicals are well studied, there are comparatively few broadly applicable catalytic methods that can convert these oxygen-rich compounds into lower-volume, higher-value chemicals. Development of effective catalytic methodologies and processes enable biomass-derived precursors to be employed in the production of personal care products, high-performance materials, and pharmaceutical ingredients.
WP3: Using and understanding catalytic oxidation processes in flow (Leads: Hintermair (Bath), Muldoon (QUB))
Oxidation reactions are common key steps in the production of many important chemicals including healthcare products, plasticisers, fragrance and flavour molecules as well as pharmaceuticals and agrichemicals. Nonetheless, oxidation reactions still pose a significant challenge on industrial scale as current methods are relatively inefficient. A detailed understanding of the underlying principles and current limitations of oxidation catalysis, i.e. addressing issues of O2 activation, the role of additives, catalyst selectivity and deactivation, and use of that knowledge to develop safe, efficient and flexible continuous flow processes promises to afford major advances in synthetic chemistry of direct industrial relevance. The UK Catalysis Hub provided an exciting opportunity bringing together catalysis experts, material scientists, chemical engineers and state-of-the-art operando spectroscopy to tackle this timely and highly rewarding challenge.
WP4: Earth-abundant metals in resource efficient catalysis (Leads: Bedford (Bristol), Webster (Bath))
Homogeneous catalysis is vital for the production of medium-sized molecules that our society depends on, such as pharmaceuticals, fine chemicals, materials and agrochemicals. By far the most widely exploited catalysts are based on platinum group metals (PGMs), however, their routine use is ultimately limited by their high cost, the high environmental impact of their extraction, increasing competition for their use from the automotive and electronics sectors and, perhaps most importantly, by their relatively high toxicity. The latter is particularly relevant to the production of pharmaceuticals where the PGM content in active pharmaceutical intermediates is tightly legislatively controlled to very low (ppm) levels, requiring expensive, wasteful extraction procedures. Therefore, there is a growing need to replace PGM-based catalysts with more resource-efficient analogues based on Earth-abundant metals (EAMs), a goal that will be pivotal in the development of the circular economy. Earth-abundant metals provide alternative, orthogonal reactivity to PGMs that allow us to undertake this exploration.
WP5: Keeping platform molecules in play (Lead: Garforth, Manchester)
Plastics, having transformed our society being inexpensive, lightweight, strong and durable, are now contaminating a wide range of natural terrestrial, freshwater and marine habitats. Unfortunately options are currently relatively limited to mechanical recycling or combustion for energy production, resulting in most UK plastic waste being landfilled. This effectively reduces the policy-making focus to the bottom of the waste hierarchy (reduce, reuse, recycle, recover). In this work package, plastics will be recycled and recovered generating bulk, commodity chemicals for use in industrial processes creating an alternative to the currently energy intensive thermal or catalytic cracking routes. We examined the use of heterogeneous catalysis and mechanochemical processes to address the engineering challenges associated with the transformation of plastics into a range of platform chemicals. The approach described here is synergistic with the homogeneous depolymerisation approach described in WP6, below.
WP6: New sustainable polymer architectures for high performance plastics (Leads: Buchard (Bath), Williams (Oxford))
In 2016, polymer (plastics) production exceeded 320 Mt worldwide, while in the UK, the plastics industry accounted for £7.5 billion in exports and 170,000 jobs in 2015, making it the second largest employer in UK manufacturing. The efficient production and recycling of polymers is a key challenge in the circular economy. Currently most polymers are sourced from petrochemicals, and their production consumes around 10% of annual fossil resources, a quantity projected to rise to 20% by 2050. Furthermore, the durability of fossil-based polymers represents a significant waste and environmental problem after use. Each year in the UK, out of 3.3 Mt of plastic waste collected, 820 kt ends-up in landfills, costing taxpayers around £82 M and persisting for centuries, while around 1.6 Mt of plastic waste is still escaping the collection system. Here, catalysis was a central enabling technology to develop: (i) more sustainable methods to make plastics; (ii) new polymeric materials capable of substituting petrochemicals in high value applications; and (iii) catalytic process that recycle plastic wastes into reusable monomers. The concepts of the circular economy and sustainability therefore underpin this research programme, and issues associated with manufacture (improved selectivity/efficiency), application (new block copolymer materials) and end-of-life (recycling or degradation) will be addressed. To tackle the pressing problems in sustainable polymer production, this project brought together synthetic organic and inorganic chemistry (molecular and solid state), catalysis (hetero- and homogeneous), in operando and computational studies, as well as reaction engineering and process optimisation.
WP7: Optimising bio-based platform molecules (Leads: Farmer (York), Mulholland (Bristol), Turner (Manchester))
Many of the industrial polymers, which are used today (e.g. polyurethanes, polyesters, polyamides) are manufactured on a large scale and typically use monomers derived from oil-based feedstocks (e.g. terephthalic acid, hexamethylenediamine, ethylene glycol, methylene diphenyl diisocyanate). For reasons of sustainability, and in order to minimize environmental impact, there is increasing interest in exploiting bio-based platform molecules to derive such monomers from renewable feedstocks. In this context hydroxymethyl furfural (HMF) has emerged as an attractive option since it can be derived in high yield from fructose. Indeed HMF has recently been used a precursor for commercial production of furandicarboxylic acid (FDCA) by Avantium. Recent announcements by both BASF and Dupont regarding the commercialization of FDCA-based polymers using ethylene glycol (BASF) and 1,3-propanediol (Dupont) as the diol suggest that bio-derived polymers such as poly(ethylene 2,5-furandicarboxylate), PEF are commercially viable as alternatives to aromatic polyesters such as PET.